Hydraulic systems remain one of the most essential components of many types of machinery out there including construction and agricultural equipment. Hydraulic repair: some elementary knowledge is crucial to any owner of equipment who wants to have his machinery to run longer and more efficiently. In this guide, some of the crucial information equipment owners should have about the maintenance and repair of their hydraulic system will be highlighted.
The content will include how to identify probable problems, simple troubleshooting and when to seek help from professional hydraulic repair services. When you reach the end of this article, you’ll be able to effectively address some of the most recurrent hydraulic issues, as well as, make the right decisions regarding your equipment. Whether a plant is experiencing a small, annoying leak from a seal or a large, catastrophic failure of a pump, addressing the problem before it happens can be more cost effective.
Why Hydraulic Repair is Important
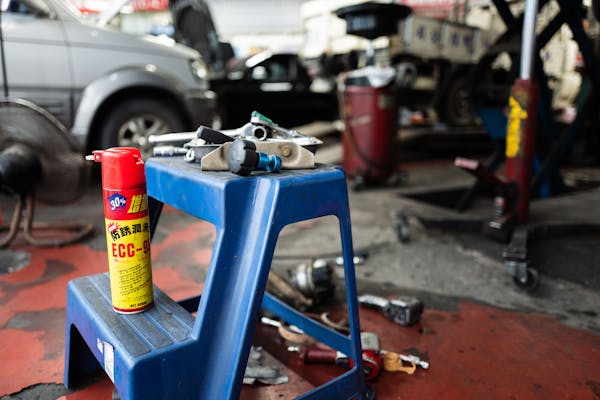
Hydraulics are a very important component in providing power solutions to different types of equipment used in biggar machinary; whether in agricultural, construction and many other industries. Such systems allow the machinery to lift and move loads and deliver well-ordered movements proficiently; however, these systems must undergo maintenance frequently and repairs as soon as they begin to show signs of failure. It is equally relevant for any piece of equipment owner to understand the logic behind hydraulic repair.
First of all, any hydraulic equipment user knows that proper maintenance of the hydraulic system and its timely repair can increase the service life of the major machinery to a great extent. If one loses sight of the minor problems like a drop of water leakage or other funny sounds, a full system collapse is soon to happen which comes at a much higher price. When you solve issues in the early stages they do not lead to a lot of losses such as extensive time off and replacement of components.
Also, hydraulic systems that are well maintained mean that energy consumption of the systems is minimal. Besides saving the environment from destruction, it also saves the company many costs hence making its operations cheaper.
Last but not the least safety must always be given a top notch priority consideration. Any hydraulic system may fail and thus is dangerous to the machine operators, service providers, and other people around. Hydraulic maintenance and troubleshooting helps you use your equipment safely and with a peace of mind none of your machinary will go up in flames as is the norm.
Related: The Best Heavy Duty Tarps in Canada: Our Top Picks for 2025
Common Signs You Need Hydraulic Repair
1. Leaks and Their Implications
Hydraulic system leaks are more than just a nuisance; they are often the first sign of underlying issues that require immediate attention. A leak could mean that seals within the system are worn or damaged, leading to loss of hydraulic fluid. This can reduce the pressure within the system, hampering its efficiency and the machinery’s ability to perform tasks. If not repaired promptly, leaks can lead to environmental hazards, increased operational costs due to wasted fluid, and potential damage to other parts of the machinery from improper lubrication or overheating. Always check for wet spots or drips under the machinery and around the hydraulic components, and address these leaks as soon as they are detected to maintain your system’s health and efficiency.
2. Changes in Noise Levels
Unusual noises coming from your hydraulic machinery are not to be ignored. Sounds like whining, knocking, or banging can indicate air in the hydraulic fluid or problems with the pump. Air can enter the system through leaks or due to low fluid levels and can cause the pump to cavitate, leading to further damage. Whining noises may also occur if the fluid viscosity is not appropriate for the system. Regularly listening to your machinery and noting any changes in the sound can help catch these issues early. Scheduling a hydraulic repair service when these noises appear can prevent more significant, costly repairs later.
3. Decrease in Performance Efficiency
If your hydraulic machinery starts to move sluggishly or responds slower than usual, it might be a sign that the system needs attention. This decrease in performance efficiency can result from various issues, including low hydraulic fluid levels, clogged filters, or worn components. A system running at reduced efficiency is not only slower but also consumes more energy and can strain other parts of the machinery, leading to premature wear. Monitoring the performance and ensuring that all hydraulic parts are in top condition can help maintain the optimal operation of your equipment.
4. Visible Wear or Damage
Visible signs of wear or damage on hydraulic components, such as hoses, fittings, and seals, are clear indicators that repairs are needed. Cracks, abrasions, or any form of visible deterioration can compromise the system’s integrity and lead to failures. Regular inspections can help identify these issues before they result in operational disruptions. Replace worn or damaged parts immediately to prevent leaks, breakdowns, and potential safety hazards associated with failing hydraulic systems.
5. Overheating
If a hydraulic system overheats, it can be a sign of various problems, including inefficient fluid levels, wrong fluid type, or excessive contamination. Overheating can degrade the hydraulic fluid quickly, which in turn reduces its effectiveness and can cause damage to the entire system. Keeping an eye on the system’s temperature during operation is crucial.
6. Erratic Operation
Hydraulic systems should operate smoothly. If you notice erratic movements or inconsistent performance, it could be due to air in the system, contamination of the fluid, or faulty valves and pumps. These issues can lead to unpredictable machinery behavior, which can be dangerous.
7. Increased Energy Consumption
An increase in the amount of energy needed to perform regular tasks is a subtle yet clear indicator of a problem. This could mean that the hydraulic system is working harder to overcome an internal problem such as internal leaks or pressure drops.
8. Fluid Discoloration or Bad Odor
Changes in the color of the hydraulic fluid or a foul odor can indicate contamination. Contaminants can include water, which causes the oil to become milky, or metal particles from component wear, which can darken the fluid. If the hydraulic oil smells burnt, it could be a sign of overheating issues.
9. Pump Cavitation
Cavitation in hydraulic pumps occurs when the volume of fluid demanded by any part of a hydraulic circuit exceeds the volume of fluid being supplied. This can cause the formation of vapor cavities which implode, causing shock waves within the pump, leading to significant damage.
Related: Different Types of Pneumatic Cylinders
Preventative Maintenance Tips
Preventative maintenance is key to ensuring your hydraulic systems run efficiently and reliably. Regular maintenance not only extends the life of your machinery but also helps prevent costly repairs and downtime. Here are essential maintenance tips every equipment owner should follow:
1. Regularly Check Hydraulic Fluid Levels: The hydraulic fluid is the lifeblood of any hydraulic system. It’s essential to regularly check the fluid levels and top them up if necessary. Low fluid levels can lead to increased wear and tear on the system’s components and reduce the system’s efficiency. Make sure to use the correct type of hydraulic fluid as specified by the manufacturer.
2. Keep the Hydraulic Fluid Clean: Contaminated fluid is a common cause of hydraulic system failures. Regularly check the cleanliness of your hydraulic fluid and replace it according to the schedule recommended by the manufacturer. Use high-quality filters to keep contaminants out of the fluid. Regularly replacing filters according to the maintenance schedule is crucial to maintaining fluid cleanliness.
3. Inspect Hoses and Fittings: Hydraulic hoses and fittings can become damaged from regular wear and tear or environmental factors. Inspect hoses for signs of cracking, brittleness, or leaks and check fittings for tightness and signs of corrosion. Replace any damaged or worn components immediately to prevent leaks and system failures.
4. Monitor System Temperature: High temperatures can degrade hydraulic fluid and damage the system. Monitor the temperature of your hydraulic system during operation and ensure it stays within the safe operating range. If your system consistently runs hot, check for issues like overloading, excessive friction, or inadequate cooling.
5. Schedule Regular Inspections: Regular inspections by a qualified technician can help catch issues before they turn into major problems. Have your hydraulic system checked annually or according to the operating hours recommended by the manufacturer. These inspections should include checks of the pump, valves, and actuators.
6. Keep a Maintenance Log: Maintain a detailed log of all maintenance and repairs performed on your hydraulic system. This log should include dates, details of the work performed, and the names of the technicians who performed the work. This will not only help you keep track of maintenance schedules but also provide valuable information in case of system failures.
7. Train Operators Properly: Ensure that all operators are properly trained on the correct use of the hydraulic machinery. Improper operation can cause unnecessary stress on the system, leading to premature wear and potential failures.
Related: Hydraulic Cylinders: A Basic to Advanced Guide
Steps to Effective Hydraulic Repair
Here’s a comprehensive step-by-step guide to ensure effective hydraulic repairs:
1. Identify the Symptoms
Before diving into any repair, first identify what symptoms your equipment is displaying. Is there a visible leak? Is the equipment operating sluggishly? Does the hydraulic fluid look milky or contain debris? Recognizing these symptoms can help pinpoint the underlying issues. This step is crucial for diagnosing the problem accurately.
2. Consult the Equipment Manual
Always refer to the manufacturer’s manual before starting any repairs. The manual contains specific maintenance schedules, part diagrams, and specifications. This information is critical to understand the system’s requirements and avoid any guesswork, which can lead to further damage.
3. Conduct a Thorough Inspection
Inspect all components of the hydraulic system including hoses, lines, seals, fittings, and the hydraulic fluid itself. Look for signs of wear, damage, or contamination. This detailed inspection should help you confirm your initial diagnosis or might reveal other hidden issues.
4. Replace or Repair Faulty Parts
Based on your inspection, replace or repair any faulty parts. Use only high-quality, compatible parts for replacements to ensure the longevity and efficiency of the repairs. For instance, if hoses are cracked or leaking, replace them with new ones that meet or exceed the system’s pressure requirements. If the issue is with a component like a pump or valve, consider whether it is more cost-effective to repair or replace it.
5. Flush the System
After replacing parts, it’s essential to flush the hydraulic system to remove any contaminants that could cause future failures. Contamination is one of the leading causes of hydraulic system breakdowns, so this step is critical.
6. Refill Hydraulic Fluid
Once the system is clean and all parts are repaired or replaced, refill the system with fresh hydraulic fluid. Ensure you use the correct type of fluid, as stated in the manufacturer’s manual. Incorrect fluid can damage the system and reduce its efficiency.
7. Test the Equipment
After the repairs are complete and the system has been reassembled, perform a comprehensive test to ensure everything is working correctly. Monitor for any leaks or unusual noises and check the response times of the hydraulic equipment. This testing phase is crucial to ensure that all repairs have been successful and the system is safe to use.
By following these steps, you can ensure that hydraulic repairs are carried out effectively, enhancing the reliability and lifespan of your hydraulic equipment. Remember, while some repairs may seem straightforward, hydraulic systems are complex, and sometimes involving a professional technician is the best course of action to ensure the work is done safely and effectively.
Related: Different Types of Hydraulic Pumps
Hydraulic Repair Services in Canada
The extensive use of hydraulic machinery across various sectors necessitates the availability of proficient hydraulic repair services. Efficient repairs are crucial for minimizing downtime, extending equipment life, and maintaining productivity. Companies should prioritize services that offer detailed diagnostics, quality replacements, and comprehensive maintenance. Regular inspections are essential to detect and address issues like leaks, wear, noise changes, and performance inefficiencies before they lead to major system failures.
At Delange’s Industries, we understand the critical nature of hydraulic systems in your operations. Our experienced technicians are equipped with the latest tools and technology to provide top-tier hydraulic repair services across Canada. We specialize in diagnosing complex problems, performing precise repairs, and offering preventative maintenance solutions that keep your equipment running at peak performance. Whether you’re dealing with routine wear and tear or emergency breakdowns, Delange’s Industries is your reliable partner for all hydraulic repair needs, ensuring your operations continue smoothly with minimal interruptions.