The use of air pressure to move things with force. They come in many shapes and sizes, each suited for different tasks. In this blog, we’ll share 40 different types of pneumatic cylinders available and how they can be used in various industries across Canada. No matter if you’re involved in manufacturing, engineering, or automation, understanding these cylinders will help you choose the right one for your needs. Let’s dive into the details and make learning about pneumatic cylinders easy and fun!
What is Pneumatic Cylinders
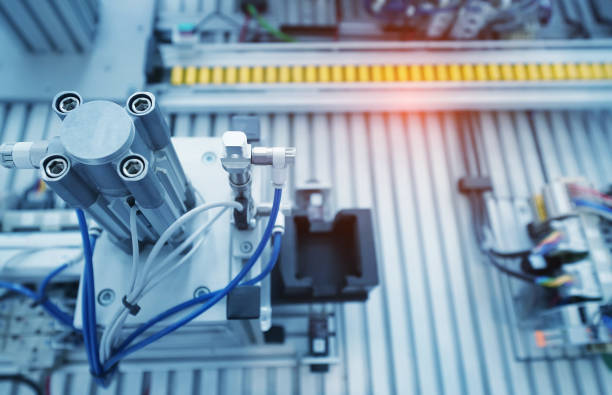
They are mechanical devices that use compressed air to produce force in a pushing, pulling, or lifting motion. Essentially, these cylinders are the muscles of many machines, enabling them to perform a variety of automated tasks efficiently.
Pneumatic cylinders come in two main types: single-acting and double-acting. Single-acting cylinders use air pressure to move a piston in one direction and a spring to return it back when the air is released. This type is great for simple tasks that require movement in one direction only.
Double-acting cylinders, on the other hand, can move the piston in both directions because they can apply air pressure from both sides. This makes them suitable for more complex tasks that require forceful movement in two directions, such as in assembly lines and automation setups.
The design of these cylinders allows for quick, safe, and reliable operation, making them ideal for high-speed machinery applications. They are widely used across various industries to automate the movement of heavy or repetitive loads.
Understanding how pneumatic cylinders work can help in selecting the right type for specific industrial tasks, ensuring efficiency and effectiveness in automated processes. They are key components in modern machinery, helping industries to achieve precision and speed in their operations.
Related: Different Types of Hydraulic Seals
40 Types of Pneumatic Cylinders
Single-Acting Cylinder
Single-acting cylinders are a basic type of pneumatic cylinder. They use air pressure to create motion in one direction and a spring to move back to the original position. This kind of cylinder is great for jobs where you only need a push or a pull in one direction, like lifting a gate or pressing a button. Because they are simple, they’re not only easy to use but also cost less and take up less space. This makes them perfect for small machines or systems where you don’t need very complex movements.
Double-Acting Cylinder
Double-acting cylinders can move in two directions. They use air pressure to move the piston out and another burst of air to pull it back in. This makes them more versatile than single-acting cylinders. You’ll find these cylinders at work in more complex machinery like manufacturing robots or in applications where precise movement control is needed. Since they require air to move both ways, they are a bit more complex and costly but are ideal for tasks that require repeated and precise movements.
Telescoping Cylinder
Telescoping cylinders are made up of several cylinders nested inside each other, similar to sections of a telescope. This design allows them to provide a very long extension while being compact when retracted. They are perfect for use in areas where space is limited but a long range of motion is needed, like in dump trucks or large industrial machinery. Telescoping cylinders can be either single or double-acting and are valued for their ability to extend much further than a standard cylinder of the same size.
Rodless Cylinder
Rodless cylinders differ from traditional cylinders as they don’t have a rod outside the cylinder body that extends and retracts. Instead, they use a magnetic or mechanical coupling to move a load along a track that is as long as the cylinder itself. This unique design is useful in environments where space is a constraint and where external moving parts might interfere with other machinery. They are often used in manufacturing lines or in automated warehousing systems where space efficiency and clean operation are important.
Compact Cylinder
Compact cylinders are designed to fit into tight spaces without sacrificing power. These cylinders are shorter and often more robust than standard cylinders, making them ideal for small-scale applications where space is at a premium but strong force is still needed. They are commonly used in robotics, automated assembly operations, and places where machinery needs to be as compact as possible. Despite their small size, they can provide the necessary force for lifting, pushing, or moving heavy items within compact setups.
Twin Rod Cylinder
Twin rod cylinders are designed with two parallel rods that provide stability and prevent the cylinder from twisting. This makes them perfect for precise guiding of loads, especially in applications where alignment is critical, such as in material handling or automated assembly processes. The dual rods help to handle side loads better, making the twin rod cylinder a reliable choice for high-precision tasks. These cylinders are commonly used in settings where space is limited but where accuracy and stability are needed.
Guided Cylinder
Guided cylinders, or guided air cylinders, are equipped with guide rods that are fixed to the moving piston and pass through the cylinder body. This design helps to resist non-linear loads and provides a more stable and accurate movement. They are ideal for applications requiring precise motion control, such as in robotic arms or fixtures that need to maintain a specific path without deviation. Guided cylinders are valuable in assembly operations where multiple movements need to be coordinated with high precision.
Rotary Actuator Cylinder
Rotary actuator cylinders convert compressed air into rotary motion. They are used in applications where angular movement is required, such as turning gears, opening valves, or manipulating robotic arms. These cylinders can provide a range of motion from a few degrees to complete turns, depending on the setup. They are compact, efficient, and can be easily integrated into more complex mechanical systems. Rotary actuators are commonly used in packaging and manufacturing processes where precise, controlled rotational movement is essential.
Cushioned Cylinder
Cushioned cylinders are equipped with end-of-stroke cushions that help reduce the impact and noise when the piston reaches the ends of the cylinder. This cushioning not only protects the cylinder and prolongs its life but also minimizes the vibration and shock to the attached equipment. These cylinders are particularly useful in heavy machinery and industrial applications where the reduction of mechanical stress is critical. Cushioned cylinders are a smart choice for any setup that involves high-speed operations or where the piston must halt suddenly.
Through Rod Cylinder
Through rod cylinders have a rod extending through both ends of the cylinder, allowing for equal force and speed on both the push and pull strokes. This type of cylinder is ideal for applications where equal displacement is required on both sides of the piston, such as clamping systems or when synchronized movement of two loads is necessary. Through rod cylinders are versatile and can be mounted in various ways, making them suitable for a wide range of industrial applications.
Tandem Cylinder
Tandem cylinders are essentially two cylinders combined into one. They’re designed this way to double the force output without increasing the size of the bore or switching to a cylinder with a much larger bore. This is particularly useful in applications where space is a constraint but a high force is required. By using two pistons in a single cylinder body, tandem cylinders can generate twice the force of a single piston using the same air pressure. This makes them ideal for heavy-duty operations like pressing or lifting in industrial environments.
Bellows Cylinder
Bellows cylinders are different from your typical pneumatic cylinders. They use a bellows instead of a piston to move the load. The bellows expands and contracts as air is pumped in and out, creating movement. This type of cylinder is great for providing gentle, controlled motion and is often used in applications requiring low force but high accuracy, such as in light material handling or precise positioning tasks. They are also highly durable and can operate without lubrication, making them suitable for cleanroom applications.
Impact Cylinder
Impact cylinders are built to deliver a high-impact force at high speed. They are specifically designed for applications requiring a significant amount of energy to be transferred in a short burst, such as punching, stamping, or riveting. These cylinders incorporate built-in cushioning to absorb the shock and protect the cylinder from damage during the impact. This makes them robust and reliable for tough industrial tasks where durability and high performance are critical.
Multi-position Cylinder
Multi-position cylinders have multiple pistons, allowing them to stop at several predefined positions along their stroke. This is useful in complex automation processes where the movement needs to be controlled very precisely and varied depending on the task. By using a single multi-position cylinder instead of several standard cylinders, you can save space and simplify your machinery. These cylinders are common in advanced manufacturing setups where flexibility and precision are paramount.
ISO Standard Cylinder
ISO standard cylinders are designed to meet specific International Standards Organization (ISO) specifications, ensuring compatibility and interchangeability across different systems and industries. These cylinders are built to standardized dimensions and mounting interfaces, which makes them easy to replace or integrate into existing systems without custom modifications. ISO standard cylinders are ideal for global operations where maintaining consistency and reliability in pneumatic systems is crucial. They are widely used in both general and demanding applications due to their robust design and standardization.
Clamp Cylinder
Clamp cylinders are specialized pneumatic cylinders designed to apply a clamping force. These cylinders are commonly used in applications where parts need to be held in place during a manufacturing process, such as in assembly lines or machining operations. Clamp cylinders are built to provide a strong and stable hold, ensuring that components do not move during critical operations. They are also designed to be compact, allowing them to fit into tight spaces within machinery where traditional cylinders might not be suitable.
Magnetically Coupled Cylinder
Magnetically coupled cylinders use a magnetic field rather than a physical connection to transfer force from the piston. This design allows the cylinder to be completely sealed off from its environment, making it ideal for use in clean or hazardous conditions where any leakage could be problematic. These cylinders are particularly useful in chemical processing, pharmaceutical, or food production industries, where maintaining purity and avoiding contamination is crucial. The lack of a physical connection also minimizes wear and tear, enhancing the cylinder’s lifespan.
Tie Rod Cylinder
Tie rod cylinders are robust and commonly used in industrial applications. They are constructed with tie rods stretched from one end of the cylinder to the other to provide additional strength and stability. This construction allows the cylinder to withstand high pressures and loads, making them suitable for heavy-duty operations in manufacturing, construction, and automation. Tie rod cylinders are known for their durability and reliability, making them a popular choice in sectors that require a high degree of mechanical integrity.
Low Friction Cylinder
Low friction cylinders are designed to reduce resistance during operation, leading to smoother movements and higher efficiency. These cylinders are particularly beneficial in applications requiring precise control and minimal resistance, such as in sensitive measuring or testing equipment. The reduced friction not only enhances performance but also decreases wear and extends the service life of the cylinder, making them cost-effective for industries focusing on precision and longevity in their operations.
Adjustable Stroke Cylinder
Adjustable stroke cylinders offer versatility by allowing the stroke length to be adjusted according to specific needs of an application. This flexibility makes them suitable for various tasks without the need to change cylinders for different stroke requirements. These cylinders are commonly used in production environments where machinery needs to handle different sizes of products or where space constraints require adaptable equipment. Adjustable stroke cylinders help in optimizing the workflow by accommodating various operations with a single pneumatic device.
Related: Choosing the Right Waterproof Tarp for Your Camping Trip
Stainless Steel Cylinder
Stainless steel cylinders are highly valued for their strength and resistance to corrosion. These cylinders are perfect for applications exposed to harsh environments, such as in the food processing or marine industries, where durability and cleanliness are crucial. Stainless steel provides an excellent defense against both rust and the corrosive effects of salts and chemicals. Moreover, their robust construction ensures longevity and reliability in demanding conditions, reducing maintenance costs and downtime for businesses.
Reed Switch Cylinder
Reed switch cylinders are equipped with a reed switch sensor that allows for precise control over the piston’s position. This feature is especially useful in automated systems where the exact position of the piston needs to be monitored and controlled for accurate operations. The reed switch is a magnetic sensor that can detect the presence of the piston without direct contact, offering a reliable and non-invasive method to gauge movement. These cylinders are commonly used in assembly lines and robotic applications where precision is paramount.
Non-Rotating Cylinder
Non-rotating cylinders are designed to prevent the piston rod from spinning, making them ideal for applications that require stable, linear motion without any rotation. This is achieved through the use of a square or keyed piston rod or guide shafts that keep the rod in alignment throughout its travel. Such features are essential in applications where the orientation of the load must remain constant, such as in precision tooling or when manipulating sensitive components in electronic or optical equipment.
Corrosion Resistant Cylinder
Corrosion resistant cylinders are designed to withstand environments that are prone to causing rust and degradation. These cylinders are treated with coatings or made from materials such as stainless steel or anodized aluminum, which provide an extra layer of protection against corrosive substances like chemicals, salt water, or polluted air. This makes them particularly suited for industries such as chemical processing, pharmaceuticals, and outdoor applications where conditions can be aggressive and potentially damaging.
Clean Room Cylinder
Clean room cylinders are specifically designed for use in environments where cleanliness and the prevention of contamination are critical. These cylinders are constructed with non-particle shedding materials and are often lubricated with food-grade or medical-grade lubricants. The design minimizes the risk of any contaminants escaping into the surrounding environment, making these cylinders ideal for semiconductor manufacturing, pharmaceutical processes, and any other applications where even minute levels of contamination could result in significant problems.
High Temperature Cylinder
High temperature cylinders are built to perform under extreme heat conditions. They are often used in industrial environments like metal foundries or glass manufacturing, where temperatures can soar and ordinary cylinders would fail. These cylinders are designed with special seals and materials that can withstand the heat without losing efficiency. This ensures that machinery can operate smoothly and reliably, even when things get hot. For businesses that deal with high temperatures, these cylinders are essential for maintaining continuous operations and preventing downtime.
Pancake Cylinder
Pancake cylinders are known for their compact and flat design, making them ideal for applications where space is tight. Despite their small size, they provide the force needed to perform tasks like lifting or pushing. These cylinders fit neatly into the machinery without altering the overall footprint, perfect for modern industrial applications where efficiency and space optimization are key. Pancake cylinders are commonly used in automation, robotics, and assembly operations where traditional cylinders are too bulky.
Slide Cylinder
Slide cylinders are designed to provide precise linear motion and are commonly used in applications requiring controlled movement and positioning. They feature a built-in bearing surface that guides the cylinder and prevents it from twisting or misaligning. This makes them particularly useful in tooling, machining, and material handling systems where accuracy is crucial. By ensuring smooth and straight motion, slide cylinders help in achieving high precision in automated tasks, enhancing productivity and reducing errors.
Duplex Cylinder
Duplex cylinders consist of two pistons within a single cylinder body, allowing for two stages of operation. This design can generate more force or extend longer than a single-stage cylinder of the same size, making it useful in applications where space constraints limit the size of the cylinder that can be used. Duplex cylinders are particularly effective in applications like pressing or punching, where a high force is required initially to perform the task, followed by a return stroke that may require less force.
Flanged Cylinder
Flanged cylinders have flanges fixed to the ends of the cylinder body, facilitating mounting and ensuring a secure attachment to machinery or structures. This type of mounting is particularly stable and is suited for heavy-duty applications where the cylinder must withstand large forces and vibrations without shifting. Flanged cylinders are widely used in construction equipment, heavy machinery, and industrial settings where reliability and durability are critical to maintaining operational integrity.
Related: How to Rebuild a Hydraulic Cylinder?
Position Sensing Cylinder
Position sensing cylinders are advanced devices equipped with sensors that provide real-time feedback on the position of the piston. This feature is incredibly useful in automated systems where precision is key. The sensors help ensure that the movement is accurate, allowing for fine adjustments in machinery and processes. These cylinders are vital in production lines, robotics, and other applications where the exact location of the piston affects the quality and efficiency of the operation. By integrating with control systems, position sensing cylinders enhance automation, making operations smarter and more reliable.
Profile Cylinder
Profile cylinders are named for their distinct square or rectangular profiles, which make them easy to install and integrate into machinery. The unique shape provides a stable and secure mount, reducing movement and increasing accuracy during operation. These cylinders are popular in modular systems where components need to be compact and easily adjustable. Profile cylinders are highly valued in material handling, assembly operations, and automation, where their form factor allows for streamlined integration with other system components.
Rod Guided Cylinder
Rod guided cylinders are designed to maintain perfect alignment of the piston rod during operation, preventing it from twisting or bending. This is achieved through external guides or bearings that support the rod. Such cylinders are essential in applications where lateral forces might affect the movement, such as in presses or molds. The guidance system ensures that the load is applied evenly and precisely, minimizing wear and tear and enhancing the longevity and reliability of both the cylinder and the machinery it operates.
Heavy Duty Cylinder
Heavy duty cylinders are built to withstand extreme conditions and loads. They are typically made from robust materials with reinforced structures to handle high pressures, loads, and harsh working environments. These cylinders are essential in industries like mining, construction, and metal fabrication, where durability and performance under stress are critical. Heavy duty cylinders ensure continuous operation and reliability in tough conditions, reducing downtime and maintenance costs.
Air-Oil Cylinder
Air-oil cylinders combine the smooth operation of hydraulic cylinders with the cleanliness and simplicity of pneumatic systems. These cylinders use air pressure to force oil to move the piston, providing a more controlled and stable motion than air alone. This type of cylinder is ideal for applications requiring precise speed control and smooth movement, such as in lifting equipment or automated production lines. The hybrid approach reduces the risk of contamination from hydraulic fluids, making air-oil cylinders a cleaner choice for industries focused on maintaining a clean and safe environment.
Sensor Ready Cylinder
Sensor ready cylinders are equipped to work with various sensors for monitoring position, speed, and force. These cylinders are a perfect fit for automated systems where real-time data feedback is essential for precise control. By having the capability to integrate sensors directly, these cylinders allow for streamlined setup and customization according to specific application needs. This is particularly useful in industries like manufacturing and robotics, where adjustments based on precise measurements can significantly enhance efficiency and product quality. Sensor ready cylinders help in maintaining consistency and reducing errors in processes.
Miniature Cylinder
Miniature cylinders are designed for applications where space is limited and light-duty operation is required. Despite their small size, these cylinders are powerful enough to perform tasks such as holding, lifting, or moving small objects. They are typically used in medical devices, small appliances, and electronic components manufacturing. Their compact design allows them to fit into tight spaces within machinery without compromising on functionality, making them ideal for intricate systems where precision is critical.
Repairable Cylinder
Repairable cylinders are built to be dismantled and fixed, which makes them a cost-effective option for long-term use. Unlike sealed units that need complete replacement if damaged, repairable cylinders can be opened up for maintenance and parts replacement, extending their lifespan and reducing waste. This feature is valuable in industrial environments where cylinders are subjected to wear and tear, as it allows for regular upkeep and restoration. These cylinders are commonly used in heavy machinery, automotive assembly lines, and other applications where durability and ease of maintenance are priorities.
Block Cylinder
Block cylinders have a compact, rectangular body that integrates all functional components, making them robust and easy to install. Their block-like structure provides excellent stability and resistance to vibration and shock loads, making them suitable for high-stress applications. Often used in machine tools, presses, and clamping devices, block cylinders deliver reliable performance in demanding situations. Their straightforward design simplifies assembly and maintenance, helping keep machinery operational with minimal downtime.
Pin Cylinder
Pin cylinders are specialized pneumatic cylinders designed with a pin at the end of the rod instead of the typical flat surface. This pin can be easily attached to levers, chains, or other mechanical linkages. Ideal for applications requiring a pivoting motion, pin cylinders are used in articulating joints, linkage systems, and wherever rotational movement is needed alongside linear motion. Their unique design allows for more versatile connections, making them a useful component in complex mechanical assemblies.
Bottom Line
The different types of pneumatic cylinders help you make informed choices for your industrial needs. Whether you need the push-pull action of double-acting cylinders or the compact design of rodless cylinders, each type has its specific benefits. Delanges Industries LTD is committed to providing top-tier hydraulic and pneumatic services across Canada, ensuring you get the most suitable pneumatic solutions for your operations. For more information or to learn more about our range of services, Call now at (604) 793-6999. At Delanges Industries our goal is to enhance your machinery with the best pneumatic cylinders and services in the market.