Hydraulic seals are essential for keeping hydraulic systems running smoothly. These small but mighty parts fit inside machines to stop leaks and keep fluids in place, which helps the machines work better and last longer.
There are different types of hydraulic seals, each designed for specific tasks and conditions. Knowing about these different types can help you choose the right one for your equipment.
In this blog, we’ll explore different types of hydraulic seals, focusing on their roles and materials, to help you understand which ones are best for your needs.
Different Types of Hydraulic Seals
Here’s an expanded explanation for each type of hydraulic seal, crafted to provide comprehensive and easy-to-understand content that can help your blog outrank the competition:
1. O-Rings
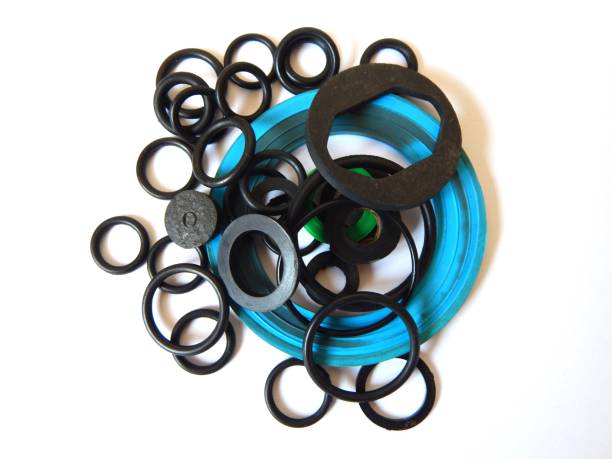
O-Rings are the most fundamental yet crucial type of hydraulic seals used across various industries. These circular seals fit into a machined groove to form a seal assembly to prevent the passage of fluids or gases between two components. O-Rings are valued for their versatility and are used in static, dynamic, hydraulic, and pneumatic applications.
Constructed usually from elastomers like Nitrile Rubber, Silicone, or Fluorocarbon, they offer excellent resistance to extreme temperatures, pressure, and chemical exposure. Their effectiveness is largely dependent on the correct sizing and material choice tailored to specific operating conditions.
2. Piston Seals
Piston seals are vital for the proper functioning of hydraulic cylinders, where they seal the cylinder bore to prevent fluid flow across the piston. This ability to maintain pressure differential is crucial for the piston’s reciprocating motion within the cylinder.
Made from materials such as polyurethane or rubber, these seals must withstand high pressures and wear while providing minimal friction. Piston seals come in various designs, including single-acting (sealing pressure from one side) and double-acting (sealing pressure from both sides), catering to different types of cylinder applications.
3. Rod Seals
Rod seals maintain the efficiency of a hydraulic system by preventing fluid from leaking out of the cylinder, thus maintaining the pressure within. These seals are placed in the gland, where the rod retracts back into the cylinder, creating a high-pressure seal against the rod. Challenges for rod seals include dealing with high dynamic pressures and adjusting to changes in side loads.
The material choice, often polyurethane or rubber, provides crucial properties such as resistance to wear and compatibility with hydraulic fluids. Proper installation and regular maintenance are key to prolonging the life of rod seals.
4. Wiper Seals
Wiper seals serve a protective function in hydraulic cylinders, preventing external contaminants such as dirt, moisture, and debris from entering the system as the rod cycles in and out of the gland. By keeping the contaminants out, wiper seals protect the internal components like rod seals and bearings from premature wear and failure.
These seals are typically made from polyurethane or rubber, offering durability against abrasion and environmental elements. Wiper seals need to be replaced regularly to ensure the integrity of the hydraulic system remains intact.
5. Guide Rings
Guide rings play a crucial role in hydraulic cylinders by preventing metal-to-metal contact, which can lead to damage and decreased efficiency. These rings help to align and guide the piston and rod within the cylinder, ensuring smooth and accurate movements.
Made from materials like PTFE or nylon, guide rings can withstand high load capacities and offer low friction characteristics. Their usage enhances the overall lifespan and performance of the hydraulic system by reducing wear and tear on critical components.
6. Buffer Seals
Buffer seals are employed in hydraulic cylinders to cope with fluctuating high pressures, enhancing the durability of the primary seals by absorbing pressure spikes. Located in the cylinder head, buffer seals complement the rod seals by providing an additional layer of leakage protection.
Typically made from materials like polyurethane or rubber, these seals are critical in applications involving high dynamic loads where they help in maintaining the stability and reliability of hydraulic systems.
7. Wear Rings
Wear rings, also known as wear bands, are used to support moving parts within a hydraulic cylinder, such as the piston or the rod. They prevent metal-to-metal contact, reducing friction and preventing scoring and galling on the cylinder walls and piston rods.
Wear rings are made from durable materials like PTFE or phenolic resin, which can endure high compressive loads and resist wear. Their application not only prolongs the service life of hydraulic components but also maintains the efficiency of the cylinder’s operation.
8. Backup Rings
Backup rings are hard rings that provide extrusion resistance and support to primary seals in high-pressure environments. Typically placed adjacent to O-Rings and other soft seals, backup rings help prevent the primary seal from being squeezed out into the clearance gap under high pressures.
Made from rigid materials such as PTFE or hard plastics, they are crucial in applications with wide temperature ranges and varying chemical exposures, ensuring the stability and longevity of seal assemblies.
9. Vee Packing
Vee Packing seals consist of multiple V-shaped layers stacked together, creating a seal that can be adjusted by changing the number of layers to suit the application’s pressure requirements. This adaptability makes Vee Packing ideal for both high and low-pressure systems across different industries. Materials commonly used include fabric-reinforced rubber and polyurethane, which provide excellent sealing properties and resistance to wear and extrusion. Vee Packing is particularly effective in older equipment where the hardware may be worn but still serviceable.
10. U-Cup Seals
U-Cup seals are named for their U-shaped profile that provides an efficient sealing force to prevent fluid leakage in hydraulic systems. The design of U-Cup seals allows for a lip that contacts the surface of the cylinder, enhancing the sealing capability under varying pressure conditions.
These seals are typically made from polyurethane or rubber, materials chosen for their flexibility, durability, and resistance to wear. U-Cup seals are versatile and can be used in both rod and piston applications, providing a cost-effective solution for maintaining the hydraulic system’s performance.
Read Also: How to Rebuild a Hydraulic Cylinder?
Materials Used in Hydraulic Seals
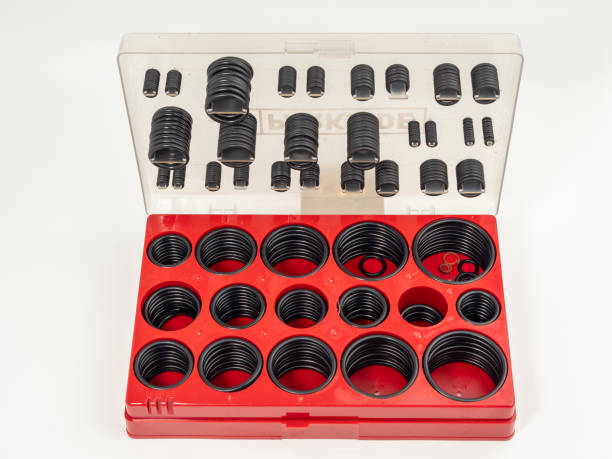
1. Polyurethane
Polyurethane is a versatile seal material favored for its exceptional resistance to wear, tear, and abrasion. This synthetic rubber combines the elasticity of rubber with the toughness and durability of metal. Polyurethane seals are particularly effective in hydraulic applications that involve high pressures and harsh operating conditions. They perform well in a range of temperatures and have excellent resistance to oil, ozone, and various chemicals, making them a popular choice for hydraulic cylinder seals where longevity and reliability are crucial.
2. Nitrile Rubber (Buna-N)
Nitrile Rubber, also known as Buna-N, is widely used in the manufacture of hydraulic seals due to its excellent resistance to petroleum-based oils and fuels. This material is composed of copolymers of acrylonitrile and butadiene, which provide good resistance to heat aging and compression.
Nitrile is effective in environments where temperatures range from -40 to 108 degrees Celsius, making it suitable for diverse hydraulic applications. Its cost-effectiveness also makes it an appealing option for many industrial applications needing voluminous sealing solutions.
3. PTFE (Teflon)
PTFE, commonly known by its brand name Teflon, is renowned for its outstanding chemical resistance and extremely low friction properties. This material is ideal for hydraulic seals exposed to a wide variety of chemical environments and extreme temperatures ranging from -200 to +250 degrees Celsius.
PTFE seals are particularly suited for applications requiring precise, minimal friction movements such as in high-performance valves and pistons. The material’s ability to maintain its properties under severe conditions ensures long-lasting seal integrity in demanding hydraulic systems.
Read Also: Different Types of Hydraulic Fittings: A Guide for Professionals
Choosing the Right Hydraulic Seal
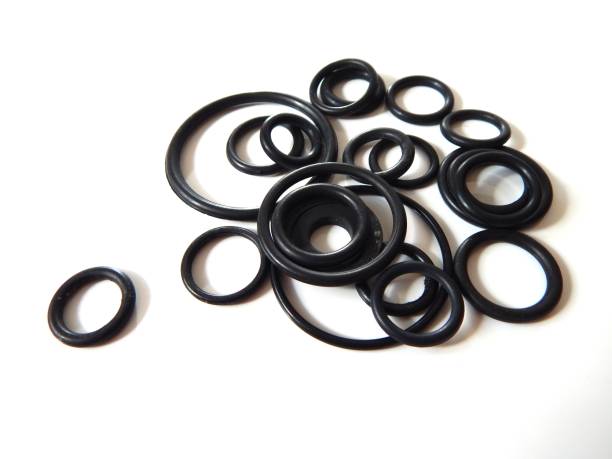
Choosing the right hydraulic seal is crucial for ensuring your hydraulic system operates efficiently and lasts longer without frequent repairs. Here are some key factors to consider when selecting the ideal seal for your needs:
Consider the Operating Conditions
Before selecting a hydraulic seal, it’s important to consider the specific conditions under which the seal will operate. This includes the temperature range, the pressure the seal will endure, and the type of fluid in the system. For instance, if your system operates under high temperatures, PTFE (Teflon) seals, known for their heat resistance, might be the best choice.
Match the Seal Material to the System’s Fluid
The compatibility of seal material with the hydraulic fluid is critical to avoid degradation and failure. Nitrile rubber is widely chosen for systems using petroleum-based fluids due to its excellent oil resistance. On the other hand, if your system uses synthetic fluids, polyurethane might be a better option due to its broader chemical compatibility.
Evaluate System Pressure and Speed
The pressure and speed at which the hydraulic system operates significantly influence the type of seal required. High-pressure systems will need seals that can handle such environments without extruding, such as those made from durable polyurethane or PTFE which offer great strength and minimal friction.
Consider the Seal’s Hardness
Seal hardness is another vital factor. Softer seals, like those made from silicone, might be great for low-pressure environments but could fail under high pressure. Harder seals can handle more pressure and are typically more durable, but they must be matched carefully to the cylinder surfaces to avoid excessive wear.
Read Also: Keep Your Hydraulic Equipment Running Smoothly with Chilliwack’s Reliable Repair Services
Maintenance Tips for Hydraulic Seals
Maintaining hydraulic seals properly is essential for keeping hydraulic systems running smoothly and preventing costly breakdowns. Here are some straightforward tips to help ensure your hydraulic seals last as long as possible:
1. Regular Inspection
Regularly check your hydraulic seals for signs of wear, tear, or damage. Look for cracks, hardening, or any deformities on the seals. Catching these issues early can prevent leaks and system failures.
2. Keep It Clean
Keeping the area around the hydraulic seals clean is crucial. Dirt, debris, or contaminants can harm seal surfaces, leading to premature wear or failure. Clean the exposed parts of the cylinder when checking or replacing seals to avoid pushing contaminants into the system.
3. Proper Installation
Ensure that hydraulic seals are installed correctly. Incorrect installation can lead to leaks, increased wear, and tear, or seal failure. Always follow manufacturer guidelines or have a professional handle the installation.
4. Use the Right Fluids
Using the correct hydraulic fluid is vital for seal longevity. Fluids that aren’t compatible with the seal material can degrade the seals quickly. Always check that the hydraulic fluid matches the specifications recommended for your seals.
5. Avoid Extreme Conditions
Protect hydraulic seals from extreme conditions where possible. Excessive heat, cold, or pressure variations can reduce the effectiveness and lifespan of hydraulic seals. If operating under harsh conditions is unavoidable, consider seals made from materials designed to withstand those extremes.
6. Regular Fluid Replacement
Change hydraulic fluids at intervals recommended by the manufacturer. Old or contaminated fluid can cause internal wear and damage to the seals. Keeping the fluid fresh helps maintain its lubricating properties and keeps the seals in good condition.
Read Also: Essential Tips for Effective Hydraulic System Maintenance
Bottom Line
Understanding the different types of hydraulic seals and their specific applications is key to maintaining the efficiency and longevity of your hydraulic systems. Whether you need O-Rings, Piston Seals, or any other type, choosing the right seal material and type is crucial for preventing leaks and reducing wear and tear. If you’re in need of fixing hydraulic seals in Chilliwack, BC, Canada, Delanges Industries is here to help you with. Our team of experts can assist you in selecting the perfect hydraulic seals for your needs, ensuring your equipment runs smoothly and effectively.