Hydraulic cylinder seals are more than just components; they are the essential elements that keep hydraulic systems running smoothly. Integral to any hydraulic repair service, these seals are key in controlling fluid movement and maintaining the right pressure. A system without proper seals is akin to a car without brakes – it simply won’t function correctly.
In our discussion, we will delve into the design and function of these seals, exploring how they prevent leaks and withstand high pressures. This is crucial knowledge for anyone involved in hydraulic repair service. We’ll also examine the different types of seals and the materials used to make them, ensuring your machinery stays in top shape for longer.
What Are Hydraulic Cylinder Seals?
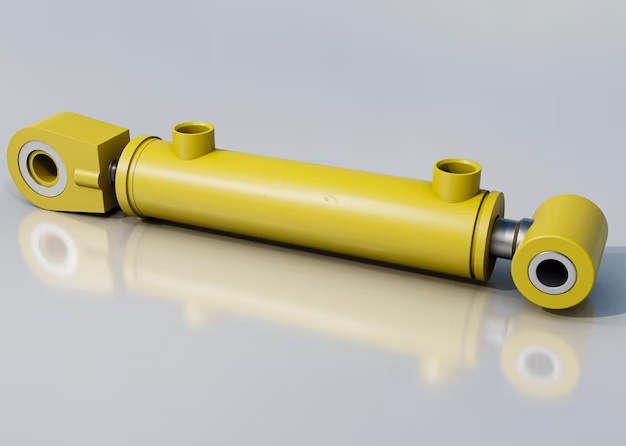
Hydraulic cylinder seals are vital parts in machinery, especially in systems that rely on hydraulics. These seals are like the guardians of a hydraulic system. They sit between different parts of a hydraulic cylinder, making sure that the fluid inside doesn’t leak out and dirt or other unwanted stuff doesn’t get in. This is super important because if the fluid leaks or gets dirty, the machine won’t work as it should.
These seals come in different shapes and are made from various materials, each chosen for its ability to handle pressure and resist wear and tear. Some are made to stay still and seal parts that don’t move, while others are designed for parts that move back and forth or spin around.
By understanding the role of these seals and choosing the right type for the job, we can make sure our machines run smoothly and last longer. This is what keeps our hydraulic systems strong and efficient, just like how a good team keeps a game going without any hiccups.
Read Also: Different Types of Hydraulic Fittings
What Are Main Functions of Hydraulic Cylinder Seals
Hydraulic cylinder seals are like the secret agents in a hydraulic system. They have some really important jobs to do. Here’s what they’re all about:
Keeping Everything in Place: They make sure the hydraulic fluid (the stuff that makes the system work) stays inside and doesn’t leak out. This is super important for the system to work right.
Blocking Dirt: Just like a superhero blocks bad guys, these seals block dirt and other tiny particles from getting into the system. This keeps everything inside clean and working well.
Handling Pressure: Whether it’s a lot of pressure or just a little, these seals can handle it. They’re designed to work under different pressures, making sure the system is always at its best.
Saving Money and Time: Because they’re so good at their job, these seals help the whole system last longer. This means less money spent on repairs and more time using the machine.
Being Tough: Made from strong materials, they can take a lot of wear and tear. This means they don’t give up easily and keep doing their job for a long time.
Adapting to Different Situations: Whether it’s a big machine or a small one, moving fast or slow, these seals can adapt and work perfectly in different situations.
So, these seals are not just another part; they’re key players in making sure hydraulic systems run smoothly and last long. They’re the unsung heroes that keep everything in check!
Read Also: Hydraulics and Pneumatics: Features, Differences, Examples, Advantages
Different Types of Seals
Hydraulic systems use several kinds of seals, each doing a special job to keep the system running well. Let’s explore these types:
Piston Seals
These seals are crucial. They fit around the piston inside the hydraulic cylinder. Their job is to stop the hydraulic oil from leaking as the piston moves up and down. This is important because if the oil leaks, the system won’t work properly.
Wiper Seals
Wiper seals are the protectors. They are located at the end of the cylinder where the rod slides in and out. Their main job is to clean off any dirt or debris from the rod. This helps prevent dirt from getting inside the cylinder, which could damage it.
Rod Seals
Rod seals are essential for maintaining the pressure inside the cylinder. They wrap tightly around the rod, preventing oil from escaping and keeping contaminants out. This ensures that the system stays pressurized and works efficiently.
Buffer Seals
These seals work alongside rod seals. They help absorb extra pressure and shock, which can happen during heavy use. This not only protects the rod seals but also helps the whole system last longer.
Wear Rings or Guide Rings
While not seals in the traditional sense, wear rings guide the piston and rod within the cylinder, preventing metal-to-metal contact, which can lead to damage and system failure.
Each type of seal is made from materials that can handle high pressure and resist wear and tear. Materials like rubber, polyurethane, and PTFE (a type of plastic) are common. The right material choice depends on the seal’s specific job and the conditions it needs to work in, like temperature and the type of hydraulic fluid used.
Understanding these different seals helps us see how they all work together in a hydraulic system. Each one has a unique role, and they need to be in good condition for the system to function correctly.
What Materials Are Used in Hydraulic Seals?
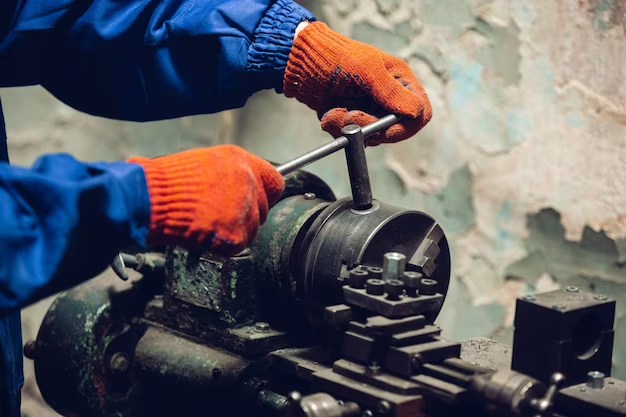
Hydraulic seals and O-rings are made from a variety of materials, each chosen for its unique properties that suit different conditions in hydraulic systems. Let’s explore the most common materials:
- Rubber: This is a popular choice for many seals due to its flexibility and ability to compress. Types like Nitrile Butadiene Rubber (NBR), Fluoroelastomer (FKM), and Hydrogenated Nitrile Butadiene Rubber (HNBR) are widely used. They are great for resisting oils and hydraulic fluids, making them a go-to for many hydraulic cylinder seals.
- Polytetrafluoroethylene (PTFE): Known for its remarkable durability, PTFE can handle extreme temperatures and pressures. It’s also resistant to chemicals, which is a big plus. Its low friction means it doesn’t need much lubrication, and it can even work well in dry conditions.
- Rigid Plastics: These are used when you need something stronger than rubber. Engineered plastics, which are tougher than standard plastics, can add extra power to the cylinder. They’re good at handling temperature and pressure changes.
- Thermoplastic Elastomers (TPEs): TPEs combine the best of plastic and rubber. They’re strong, flexible, and can keep their shape under pressure for a long time. They’re also resistant to wear and tear, making them durable choices for hydraulic seals.
Each material has its own strengths, like flexibility, strength, or resistance to chemicals and temperatures. When choosing a material for hydraulic seals, it’s important to consider what the seal will face in the hydraulic system, like the type of fluid, the range of temperatures, and the level of pressure.
Examples of Hydraulic Cylinder Applications
Hydraulic cylinders, equipped with reliable hydraulic seals and O-rings, are crucial in many machines we see and use every day. Let’s explore some common examples where these cylinders play a key role:
- Construction Machinery: Think of the heavy-duty equipment used in construction, like excavators, bulldozers, and backhoes. Hydraulic cylinders in these machines help lift heavy loads, dig, and move earth. They make it possible to do big jobs with precision and strength.
- Agricultural Equipment: In farming, hydraulic cylinders are used in tractors, harvesters, and plows. They help in tasks like plowing fields, harvesting crops, and more. These cylinders make the tough work of farming a lot easier and more efficient.
- Automotive Industry: Hydraulic cylinders are also key in the automotive industry, especially in manufacturing and maintenance. They are used in car lifts, which raise vehicles for repairs and inspection.
- Aerospace and Aviation: In the aerospace sector, these cylinders are used in the landing gear of airplanes, controlling the doors of aircraft, and even in flight simulators for pilot training.
- Manufacturing and Industrial Equipment: In factories, hydraulic cylinders are used in various machines for pressing, bending, and forming materials. They provide the force needed for manufacturing a wide range of products.
- Entertainment Industry: Surprisingly, they are also used in the entertainment industry, like in theme park rides, where they help create those thrilling movements and effects.
How Seals Affect System Integrity and Performance
Hydraulic seals and O-rings might seem like small components, but they play a vital role in the functionality of hydraulic systems. These seals are crucial in maintaining the necessary pressure within the system, much like a lid keeps the contents of a jar secure. This is essential because the hydraulic fluid, which is the lifeblood of the system, needs to be contained under pressure to ensure the system operates effectively. If there’s a leak, the system’s pressure drops, leading to inefficiency or even failure.
Beyond just keeping the fluid in, these seals are the frontline defense against contamination. They prevent dirt, dust, and other external contaminants from entering the system. This is critical because even a small amount of contamination can cause significant damage to the intricate workings of the hydraulic system. By keeping these contaminants out, the seals ensure the longevity and reliability of the system.
Another important aspect of hydraulic seals is their role in reducing wear and tear. They facilitate smooth movement between parts, minimizing friction. This not only prolongs the life of the system but also enhances its efficiency. Less friction means less effort is needed for movement, leading to lower energy consumption and improved overall performance.
Moreover, hydraulic seals are designed to adapt to various operating conditions. They are made from materials that can withstand different temperatures and pressures, making them versatile for diverse environments. Whether it’s extreme cold, intense heat, or high-pressure situations, these seals are engineered to maintain their integrity and performance.
In essence, hydraulic seals and O-rings are small yet mighty components that significantly impact the integrity and performance of hydraulic systems. Their ability to maintain pressure, prevent contamination, reduce wear and tear, and adapt to different conditions makes them indispensable in ensuring that hydraulic systems operate smoothly, efficiently, and durably.
Read Also: Essential Guide to Hydraulic Repair Services in Chilliwack
Choosing the Right Seals for Your Hydraulic Cylinder
When it comes to hydraulic systems, picking the right seals is like choosing the best players for a soccer team. Each seal has a specific role that helps the system work its best. Here’s how to choose the right hydraulic seals and O-rings for your hydraulic cylinder:
Understand the System’s Needs: First, think about what your hydraulic system does. What kind of pressure does it handle? Is it exposed to high temperatures or harsh chemicals? Knowing this helps you choose seals that can handle these conditions.
Select the Right Material: Different materials are good for different things. For example, rubber seals are flexible and great for general use. But if you’re dealing with extreme temperatures or chemicals, you might need something tougher like PTFE or specialized plastics.
Consider the Seal Type: There are various types of seals, like piston seals, rod seals, and wiper seals. Each type has a job to do, like keeping fluid in, keeping dirt out, or reducing friction. Make sure you pick the right type for each part of your cylinder.
Quality Matters: Always go for high-quality seals. They might cost a bit more, but they last longer and do a better job. This means less maintenance and fewer problems down the road.
Get Expert Advice if Needed: If you’re not sure, ask someone who knows. A professional can help you pick the perfect seals for your hydraulic cylinder, ensuring your system runs smoothly and efficiently.
Remember, the right seals make a big difference in how well your hydraulic system works. They keep everything running smoothly, reduce wear and tear, and can even save you money on repairs and energy costs. So, take your time and choose wisely!
Maintenance and Care For Cylinder Seals
Taking care of hydraulic cylinder seals is like looking after the engine of a car. Proper maintenance ensures everything runs smoothly and lasts longer. Here’s how you can maintain and care for your hydraulic cylinder seals:
Regular Inspection: Just like checking your car before a long trip, regularly inspect your hydraulic seals for any signs of wear or damage. Look for cracks, tears, or any deformation. Catching problems early can save you from bigger issues down the road.
Cleanliness is Key: Keep the area around the cylinder seals clean. Dirt and debris can cause damage to the seals, leading to leaks. Think of it as keeping your workspace tidy to avoid accidents.
Proper Installation: When installing new seals, do it carefully. Make sure they fit perfectly and are aligned correctly. It’s like putting together a model airplane – precision matters.
Use the Right Fluids: Just like using the right oil for your car, use the correct hydraulic fluid for your system. Wrong fluids can damage the seals or cause them to wear out faster.
Avoid Extreme Conditions: If possible, try to keep your hydraulic system away from extreme temperatures and environments. It’s like parking your car in the shade on a hot day to protect it.
Regular Maintenance Schedule: Set up a maintenance schedule, just like regular car services. This includes changing the fluid, checking the pressure levels, and replacing worn-out seals.
Conclusion
Hydraulic cylinder seals are not just components; they are the heartbeat of hydraulic systems. Their role in maintaining system integrity and ensuring peak performance cannot be overstated. From controlling and maintaining the pressure of hydraulic fluid to preventing contamination and leakage, these seals are pivotal in the smooth operation of various machinery and equipment.
The selection of the right seals, made from materials that can withstand specific operational stresses, is crucial. Whether it’s rubber, PTFE, or specialized plastics, each material brings unique properties that enhance the functionality and longevity of the hydraulic system. Moreover, the maintenance and care of these seals are just as important as their selection. Regular inspections, cleanliness, and proper installation go a long way in extending the life of both the seals and the hydraulic system as a whole.
Hydraulic cylinder seals may seem small, but their impact is huge. They are the unsung heroes in the world of machinery, silently ensuring that everything runs smoothly. By understanding their importance and giving them the attention they deserve, we can significantly improve the efficiency, reliability, and lifespan of our hydraulic systems.
Need expert help with your hydraulic seals? Delanges Industries in Chilliwack, BC Canada, is here to assist you with top-quality products and services.
People Also Ask
Are there special O-rings for hydraulics?
Yes, there are special O-rings designed for hydraulic systems. These O-rings are made to withstand high pressures and are often made from materials like nitrile rubber or polyurethane, which offer excellent resistance to hydraulic fluids and pressure.
What is the purpose of an O-ring in a hydraulic cylinder?
The purpose of an O-ring in a hydraulic cylinder is to create a tight seal between different components. This seal prevents hydraulic fluid from leaking and keeps contaminants out, ensuring the cylinder operates efficiently and maintains the necessary pressure.
Are nitrile O-rings good for hydraulics?
Nitrile O-rings are indeed good for hydraulic systems. They are popular due to their resistance to oils, fuels, and hydraulic fluids, as well as their ability to perform well in a range of temperatures and pressures.
What seals are used in hydraulic systems?
Hydraulic systems commonly use a variety of seals, including O-rings, piston seals, rod seals, wiper seals, and buffer seals. Each type of seal has a specific role, such as preventing fluid leakage, protecting against contamination, or reducing friction.