Hydraulic systems are powerful tools used in many machines you see every day, like diggers and lifts. These systems use liquid power to do heavy jobs easily and quickly. This blog will provide a comprehensive introduction to Hydraulic systems, principles and advantages of hydraulics.
We’ll also dive into the basic rules that make them work so well and how they’re kept running smoothly with proper repair and care. Understanding these systems can help you see just how important they are in making many tasks easier and more efficient.
What is a Hydraulic System?
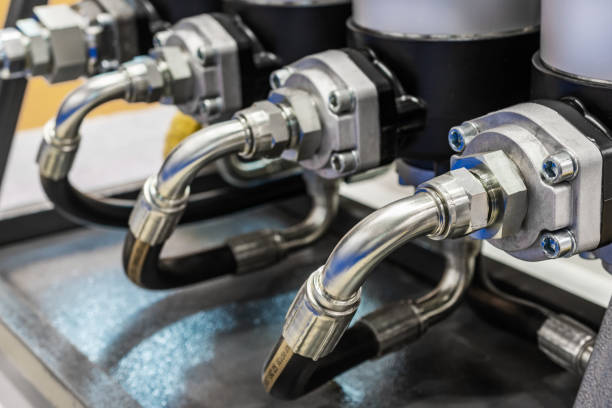
A hydraulic system is a powerful setup that uses liquid to make machines work. Unlike systems that use gears or belts, hydraulic systems use oil under pressure to move things like lift arms, press tools, or even airplane controls. This oil is pushed through small tubes and hoses, moving parts of the machine with great force and precision.
These systems are crucial in many areas. For instance, they help construction vehicles lift heavy materials and enable car brakes to stop smoothly. Because the oil doesn’t compress easily, it can transfer a lot of energy quickly, making hydraulic systems very efficient.
When these systems break or wear out, hydraulic repair is needed to keep the machines running smoothly and safely. Repair work might involve fixing leaks, changing the oil, or replacing worn-out parts.
Advantages of Hydraulic Systems
Hydraulic systems have several big advantages that make them very useful in many machines around us. Here’s why they are so important:
Strong Power
Hydraulic systems are able to lift or move very heavy things easily. This is because they use a liquid, usually oil, which is pushed under high pressure. This high pressure can move large loads, like big rocks or heavy metal parts, which would be very hard to move by hand or with other kinds of systems.
Precise Control
With hydraulic systems , you can control machines very accurately. Whether you need to make small adjustments or need precise movements, hydraulic systems allow you to manage every movement smoothly. This precise control is especially important in tasks where you need careful handling, like in precise manufacturing processes or when using heavy machinery.
Speed
Hydraulics are quick to respond. When you press a button, the system reacts almost instantly, allowing machines to start or stop right away. This quick action is useful in many situations, from emergency stops in vehicles to fast movements in robotic arms.
Reliability
These systems are built to last. They work well in different environments, whether it’s extremely cold, very dusty, or super wet. Hydraulic systems keep working even when other types of systems might break down, which means they are dependable for long-term use in tough conditions.
Easy to Repair
When hydraulic systems do need repairs, fixing them is generally straightforward. The parts that might need to be replaced, like seals or hoses, are usually easy to access and change. This means machines can be fixed quickly and get back to work, reducing downtime and saving money on repairs.
Read Also: Essential Tips for Effective Hydraulic System Maintenance
Principles of Hydraulic Systems
Pascal’s Law
This principle is at the heart of how hydraulic systems work. It says that when you press down on a liquid in a closed space, the pressure spreads equally in all directions. So, when you push on the liquid in one part of the system, it creates the same amount of force elsewhere. This allows small actions, like pushing a lever, to move heavy loads, which is essential in machinery like excavators and car brakes.
Force Multiplication
Hydraulics can multiply your effort, making it possible to lift or move big things with a small amount of force. For example, pushing lightly on a pedal or handle can result in a large force being exerted by the machine. This is because the system uses larger and smaller cylinders connected by hydraulic fluid—pushing on the smaller one increases the force that is applied by the larger one.
Hydraulic Fluid
The fluid used in these systems, usually oil, is very important because it does not compress under pressure. This means it can transfer force very effectively and smoothly across the system. The fluid also helps to lubricate the parts to reduce wear and tear, and it helps keep the system clean by carrying away contaminants.
Control Valves
Control is key in hydraulic systems. Valves help to direct the flow of the hydraulic fluid, allowing the system to perform different actions based on what the operator needs. These valves can start, stop, and direct the flow of the hydraulic fluid, making precise movements possible and ensuring the machine operates smoothly.
Safety and Efficiency
Hydraulic systems are designed to be safe and efficient. They have built-in mechanisms to manage the pressure to avoid overloading the system, which protects both the machine and the operator. Efficient design also means that these systems use less energy to do more work, making them environmentally friendly and cost-effective.
Read Also: Different Types of Hydraulic Fittings: A Professional Guide
Applications of Hydraulic Systems
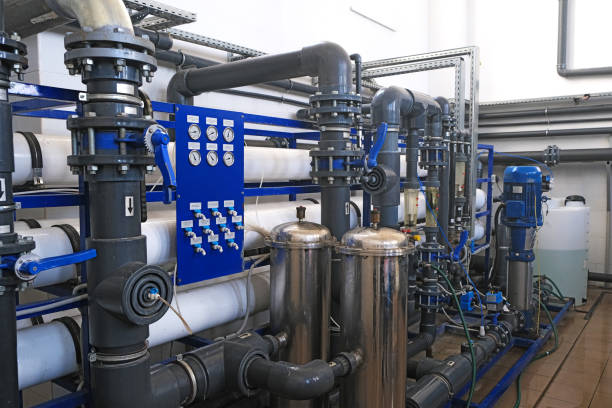
Hydraulic systems are incredibly important in many machines and industries around the world. They use a fluid to power various parts of machinery, making them able to do heavy work with ease. Here’s a closer look at how hydraulic systems are used in different fields:
1. Construction Equipment
In the construction industry, hydraulic systems are essential. Machines like excavators, bulldozers, and backhoes all use hydraulics to perform tasks that involve heavy lifting and digging. For instance, an excavator uses hydraulic power to operate its arm and bucket to dig up soil or lift heavy objects. This system allows the machine to perform heavy-duty tasks with precision and strength, which manual labor or other types of machinery would struggle to accomplish efficiently.
2. Automotive Industry
Hydraulic systems play a critical role in the automotive sector, particularly in the braking and steering systems of vehicles. When you press the brake pedal in your car, hydraulic fluid is pushed through a series of lines to the brake pads at each wheel. The pressure from the fluid enables the pads to clamp onto the wheels, slowing down or stopping the car. This system ensures that a small effort from the driver can translate into a significant action, like stopping a fast-moving vehicle safely.
3. Manufacturing Machinery
In manufacturing settings, hydraulic systems are found in various machines such as presses that mold, shape, or cut materials, and assembly machines that require precise movements. These systems are favored because they can generate a lot of power through small, controlled movements. This ability makes them perfect for tasks that need both strength and accuracy, like pressing a piece of metal into a specific shape or lifting heavy parts into place on an assembly line.
4. Aerospace Applications
Aircraft also rely heavily on hydraulic systems for several critical operations. These include controlling the movement of wings and flaps, which helps the pilot maneuver the plane, and operating the landing gear. Hydraulic systems in airplanes must be extremely reliable and precise, as even a minor failure can be catastrophic. The power and reliability of hydraulics make them ideal for these uses, where failure is not an option.
5. Amusement Park Rides
Amusement parks use hydraulic systems to operate many of their rides, especially those that involve lifting or high-speed movements. Hydraulic power helps to ensure these rides can carry heavy loads of passengers and operate smoothly. For example, hydraulic systems may be used to raise a ride to a great height quickly or to control the speed of a roller coaster. The use of hydraulics in rides is critical for safety, making sure that the thrill and excitement remain safe for all riders.
Regular maintenance and hydraulic repair are key to keeping these systems running effectively and safely. Without proper care, hydraulic systems can wear out, leading to breakdowns or accidents. Maintenance involves checking the hydraulic fluid for signs of aging or contamination, replacing worn-out parts, and making sure all components are in good working order.
Overall, hydraulic systems are a cornerstone of modern machinery and technology. Their ability to exert tremendous force with precise control and reliability makes them indispensable in many sectors. Whether lifting heavy loads, shaping materials, controlling massive aircraft, or ensuring the safety of fun rides, hydraulics are fundamental to achieving these tasks efficiently and safely.
Read Also: The Role of Hydraulic Cylinder Seals in System Integrity and Performance
Components of Hydraulic Systems
Hydraulic systems are made up of several key components that work together to move and control machinery smoothly and powerfully. Understanding these parts can help anyone see how these systems manage such heavy tasks:
Hydraulic Pumps and Oils
Hydraulic pumps are the heart of the hydraulic system. They move hydraulic oil, the system’s lifeblood, through the machine. This oil transmits the energy needed to do tasks from one part of the system to another. Think of the pump as a water faucet but for oil; when it turns on, it pushes oil through pipes to get the machine moving. The oil itself is also crucial because it lubricates the system, helping everything move smoothly without too much wear and tear, and keeps the system clean by carrying away dirt and debris.
Directional Control Valves
Directional control valves direct the flow of the hydraulic oil within the system. You can compare them to traffic officers at intersections, deciding which way the oil (or traffic) should go. These valves can switch the path of the flow, allowing the system to perform different functions, like lifting or lowering a loader’s arm. The ability to control the direction of the flow precisely is vital for machines that need to perform complex sequences of operations.
Flow Control Valves and Pressure Reducing Valve
Flow control valves adjust the speed of the hydraulic oil, while pressure reducing valves manage the pressure within the hydraulic system. These valves ensure that the hydraulic oil moves at the right speed and pressure, much like controlling the water coming out of a hose. This control is important for maintaining the efficiency of the system and preventing damage from too much pressure or flow that is too fast, which could lead to parts wearing out quickly.
Hydraulic Actuators
Hydraulic actuators are the muscles of the hydraulic system. They convert the hydraulic energy into mechanical force. This might mean pushing, pulling, lifting, or pressing—whatever the job needs. Actuators come in various types, such as cylinders and motors, and are used depending on the type of motion needed. For instance, hydraulic cylinders create a back-and-forth movement, useful for devices like hydraulic presses, while hydraulic motors support continuous rotation, like turning the wheels of a conveyor belt.
Read Also: Keep Your Hydraulic Equipment Running Smoothly with Chilliwack’s Reliable Repair Services
Hydraulic Safety Precautions and Hydraulic System Maintenance
Hydraulic systems are powerful tools, but they can be dangerous if not handled properly. To ensure safety while using these systems, follow these guidelines:
Regular Inspections
Conduct thorough inspections of the hydraulic systems regularly. Look for any signs of wear, damage, or leaks. Small issues like loose fittings or cracked hoses can lead to bigger problems if they’re not addressed quickly.
Check all seals and valves to ensure they are intact and functioning correctly. Leaks can be a sign of seal failure and should be repaired immediately to prevent accidents.
Use Proper Tools and Equipment
Always use the correct tools and equipment when working on hydraulic systems. Improper tools can damage the system components or fail to fix the issue, leading to accidents or system failures.
Ensure that the tools are in good condition and suitable for the specific job.
Safety Training
Anyone operating or maintaining hydraulic systems should receive proper training. They should understand how the systems work, the risks involved, and the safety procedures to follow.
Regular training updates can help keep everyone aware of the best practices and any new safety protocols.
Emergency Procedures
Develop and clearly communicate emergency procedures for dealing with hydraulic failures or accidents. Knowing what to do in an emergency can prevent injuries and minimize damage to the system.
Include steps to safely shut down the system and evacuate the area if needed.
Hydraulic System Maintenance
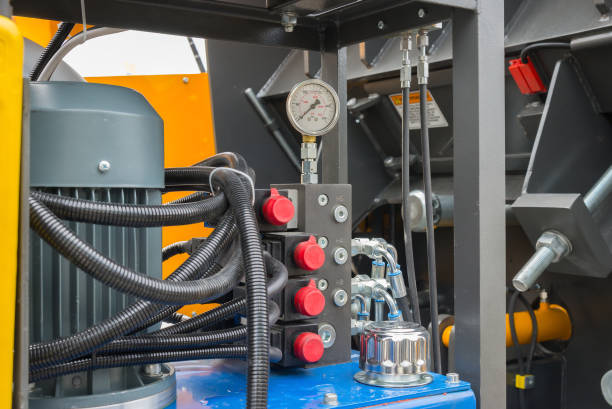
Regular maintenance is crucial for keeping hydraulic systems running smoothly and preventing breakdowns. Here are some key maintenance practices:
Regular Fluid Checks
Monitor the level and condition of the hydraulic fluid. Low fluid levels can lead to system inefficiency and damage, while dirty or contaminated fluid can cause wear and tear on components.
Change the hydraulic fluid according to the manufacturer’s guidelines or if it becomes contaminated.
Change Filters Regularly
Hydraulic systems have filters to remove contaminants from the fluid. These filters should be checked regularly and changed when necessary to ensure they are effective.
A clogged filter can lead to increased wear on the system, as dirty fluid continues to circulate.
Preventive Maintenance Schedule
Set up a preventive maintenance schedule based on the manufacturer’s recommendations and stick to it. This involves regular checks of all parts of the system, including pumps, valves, hoses, and actuators.
This schedule should include routine cleaning, adjustments, and replacements as needed.
Prompt Repairs
Address any repairs immediately. Ignoring small problems can lead to more significant issues that might cause the system to fail and could be much more expensive to fix.
Keeping spare parts on hand can help reduce downtime during repairs.
System Upgrades
Periodically review the system’s performance and consider upgrades or replacements for outdated or inefficient components. This can improve system efficiency and safety.
Hydraulic Repair Services in Chilliwack, BC Canada
In Chilliwack, BC, Canada, Delanges Industries offers expert hydraulic repair services tailored to keep your hydraulic systems running smoothly. We specialize in diagnosing and fixing a wide range of hydraulic issues, from leaky seals to complete system overhauls.
Our team of skilled technicians uses the latest tools and techniques to ensure your equipment is repaired quickly and efficiently, minimizing downtime and maintaining productivity. Whether you’re in construction, manufacturing, or any industry relying on hydraulic machinery, you can count on us to provide reliable and effective repair solutions right here in Chilliwack.
People Also Ask
What do Hydraulic Repair Services do?
These services fix parts of the system that might be broken or worn out. For example, they can replace leaky hoses, fix broken pumps, and make sure valves are working right. This is important because even a small issue, like a leak, can cause big problems if it’s not fixed quickly.
Why are they so important?
Hydraulic systems need to work smoothly because they do heavy lifting and moving. If they break down, it could stop all the work and be very costly. Regular checks and repairs keep these systems running well and prevent big problems.
What to look for in Hydraulic Repair Services?
Good repair services have skilled mechanics who know a lot about hydraulic systems. They should also respond quickly when there’s a problem and use good quality parts for repairs. Choosing a reliable service means your hydraulic system will be taken care of well, keeping it running smoothly and avoiding long downtimes.