Have you ever thought how giant machines lift heavy loads or why some tools can push and pull with great force? The secret is hydraulic systems! These systems use liquids to make things move fast and with a lot of power.
In this blog, we’ll learn how these amazing systems work and how you can make them even better. Whether you need to fix or improve a hydraulic system, you’ll find helpful tips here. So let’s explore hydraulics and learn how to make them faster and stronger!
What Are Hydraulic Systems?
Hydraulic systems are powerful tools used in machinery to move and lift heavy objects. These systems operate by transferring force through liquid—usually oil—inside a sealed setup of pumps and cylinders. This process allows for controlled and strong movements that can be applied in various fields, from automotive brakes to industrial manufacturing equipment.
The beauty of hydraulic systems lies in their ability to generate immense force with minimal mechanical input, making them essential for tasks that require precision and power. Understanding these systems is key for anyone looking to enhance the efficiency and capability of their machinery.
Read Also: Preventative Hydraulic Maintenance and Repair in Chilliwack, BC Canada
Key Components of Hydraulic Systems
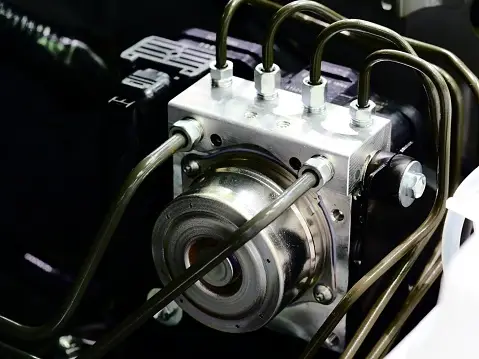
1. Hydraulic Fluid
Hydraulic fluid is more than just a medium for power transfer; it also plays a pivotal role in lubrication, heat transfer, and contamination control within the system. By maintaining the fluid under pressure, hydraulic systems can efficiently transmit energy to various parts of the machine. Choosing the right fluid is critical as it affects the system’s performance, responsiveness, and longevity.
2. Hydraulic Pump
The pump acts as the heart of the hydraulic system. It converts mechanical energy from a motor into hydraulic energy by pushing the hydraulic fluid into the system under pressure. This process is vital for the system to function as it provides the force needed for the fluid to travel throughout the system and actuate the machinery.
3. Reservoir
The reservoir holds the hydraulic fluid and plays multiple critical roles. It allows contaminants to settle, aids in cooling the fluid, and helps to maintain proper fluid levels in the system. Ensuring that the reservoir is properly maintained and that the fluid levels are adequate can significantly affect the system’s efficiency and prevent mechanical failures.
Read Also: Essential Tips for Effective Hydraulic System Maintenance
4. Hydraulic Valves
Hydraulic valves control the flow and pressure of the hydraulic fluid, directing it to specific parts of the system at precise times. They are essential for managing the performance of the system, allowing for the adjustment of flow rates and system pressure, which are crucial for different operations and machinery efficiency.
5. Actuators
Actuators are the output force of the hydraulic system, where the hydraulic energy is converted back into mechanical energy. They come in two main types: hydraulic cylinders, which produce linear motion, and hydraulic motors, which produce rotational motion. Actuators are fundamental for performing the work in hydraulic applications, from lifting heavy loads to operating complex machinery movements.
6. Hydraulic Hoses and Pipes
Hoses and pipes are the conduits for the hydraulic fluid, connecting the various components of the system. These elements must withstand high pressures and be flexible enough to fit into the machinery without leaking. The integrity of hoses and pipes is crucial as any leak can lead to decreased efficiency and system failure.
7. Hydraulic Filters
Filters are crucial for prolonging the life of a hydraulic system. They remove particulate contaminants and degradation products from the hydraulic fluid, which can cause significant wear and tear on the hydraulic components. Regular maintenance and replacement of filters are essential for keeping the system clean and functioning optimally.
8. Seals and Fittings
Seals and fittings ensure that the hydraulic system is airtight and watertight, preventing leaks and maintaining pressure within the system. Proper seals and secure fittings are critical for system efficiency and preventing fluid loss, which can lead to system failure and increased operational costs.
Read Also: How to Repair a Hydraulic Hose in Just 6 Steps
8 Strategies to Boost Hydraulic Systems for Speed & Force
1. Select the Right Components
To make a hydraulic system work best, picking the right parts is crucial. Think of it like choosing players for a soccer team; you need the right roles filled to play well. In hydraulic systems, components like pumps, valves, and cylinders must match the job’s needs. For example, a bigger pump can handle more fluid, helping the system act faster and stronger. Always choose components that fit the system’s overall design and performance goals.
2. Use High-Performance Fluids
The fluid in a hydraulic system is like the blood in our bodies—it needs to be healthy to keep the system running smoothly. High-performance fluids reduce friction and wear, resist heat, and keep the system clean. Using the best fluid can mean less downtime and fewer repairs, making everything more efficient. Always check the fluid’s quality and change it as needed to ensure it’s helping, not hurting, the system.
3. Optimize System Design
A well-designed hydraulic system is streamlined and balanced, much like a well-organized workspace. By optimizing the layout and connection of components, the system can perform at its peak. This includes arranging hoses and pipes efficiently to reduce resistance and ensuring all parts are accessible for maintenance. A good design minimizes losses and maximizes the transfer of power, crucial for achieving high speed and force.
4. Implement Efficient Control Systems
Control systems are the brains of the operation, dictating how and when the system reacts. Implementing efficient control systems, such as advanced servo and proportional valves, allows for precise adjustments in flow and pressure, critical for tasks that require quick and powerful action. These sophisticated controls enable the hydraulic system to achieve precise movements, essential for high-performance applications. Upgrading to smarter control systems can transform a hydraulic system’s functionality, making it more dynamic and responsive.
Read Also: Different Types of Hydraulic Seals
5. Employ High-Performance Actuators
High-performance actuators are critical for powerful and precise movements in hydraulic systems. These actuators, which convert hydraulic energy into mechanical force, must be robust enough to handle high pressures and fast actions. Choosing actuators designed for high performance ensures that they can withstand demanding tasks without failing, resulting in more reliable and efficient operations. When upgrading, consider actuators that offer improved durability and faster response times to enhance overall system performance.
6. Ensure Proper Maintenance
Regular maintenance is the key to keeping hydraulic systems running smoothly. This involves regularly checking and replacing hydraulic fluid, inspecting hoses and connections for leaks, and ensuring that all components are in good working order. Scheduled maintenance prevents unexpected breakdowns and prolongs the life of the system. It’s like taking care of a car; routine checks and timely repairs keep it running efficiently and safely.
7. Consider Energy Recovery Systems
Integrating energy recovery systems into hydraulic setups can significantly increase efficiency. These systems capture and reuse the energy typically lost during operations, such as through heat or mechanical work. By reusing this energy, the overall energy consumption of the system decreases, making it more sustainable and cost-effective. Energy recovery is especially valuable in systems that require frequent and intense operations, as it enhances performance while reducing environmental impact.
Read Also: How to Use Tarp Repair Tape
8. Perform Comprehensive Testing
Thorough testing of hydraulic systems is essential to ensure they operate safely and effectively. This includes stress tests, performance evaluations, and routine operational checks. Testing helps identify potential issues before they lead to failures, ensuring the system is optimized for high-speed and high-force tasks. Think of testing as a rehearsal for a play—it helps ensure everything runs smoothly when it’s showtime, providing confidence in the system’s capability to perform under pressure.
Wrapping Up
Optimizing your hydraulic system for high-speed and high-force actuation is essential for top performance. By employing high-performance actuators, ensuring regular maintenance, integrating energy recovery systems, and conducting comprehensive testing, you can significantly enhance the efficiency and reliability of your operations. At Delanges Industries, we specialize in helping you achieve these improvements. Our expert team offers tailored solutions and top-notch hydraulic repair services to ensure your systems meet the highest standards.