Hydraulic pumps are vital components in many machines used in construction, manufacturing, and transportation. They operate by moving hydraulic fluid through systems to power various functions of heavy machinery.
There are several types of hydraulic pumps, each designed to meet specific requirements and operating conditions. In this blog, we’ll explore the different types of hydraulic pumps, including gear, vane, and piston pumps. Understanding how each type works and where it’s best applied can help in selecting the right pump for the job, ensuring efficiency and reliability in demanding environments.
1. Gear Pumps
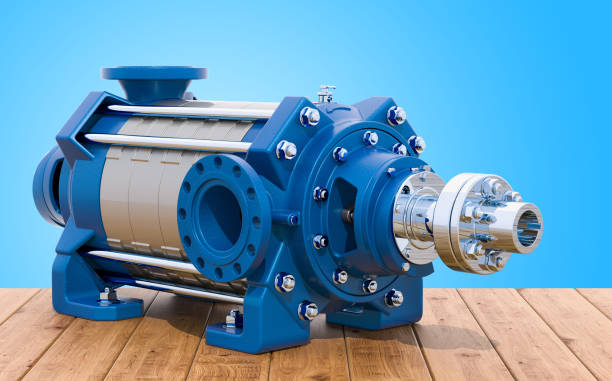
Gear pumps are among the most widely used types of hydraulic pumps in various industrial applications. These pumps play a critical role in hydraulic systems by creating pressure that moves fluid through the system, which in turn powers different types of machinery.
Gear pumps are favored for their reliability, simplicity, and ability to handle a range of viscosities. Let’s dive deeper into how gear pumps work and explore their two main types: external gear pumps and internal gear pumps.
External Gear Pumps
External gear pumps feature two identical gears that mesh together. One gear is driven by the motor, which then drives the other gear. The gears rotate against each other, and as they turn, fluid on the inlet side is scooped up between the teeth of the gears and the walls of the pump casing. This fluid is carried around the exterior of the gears to the outlet side, where it is forced out of the pump as the gear teeth mesh completely and displace the fluid.
These pumps are particularly valued for their robustness and efficiency in generating high pressures. Commonly used in automotive applications such as power steering systems, transmissions, and fuel transfer pumps, external gear pumps are also prevalent in the manufacturing sector for fluid power applications. Their simple and compact design makes them easy to maintain, and they can operate efficiently at high rotational speeds.
The primary advantage of external gear pumps is their simplicity, which results in a cost-effective and long-lasting pump solution for many industrial applications. They are capable of handling relatively thin but also moderately viscous fluids, making them quite versatile.
Related: Hydraulic Cylinders: A Basic to Advanced Guide
Internal Gear Pumps
Internal gear pumps are slightly more complex and consist of two gears as well; however, the configuration is different. An internal gear pump uses an inner and an outer gear, but the inner gear is smaller and has fewer teeth. The inner gear is positioned inside the outer gear and rotates eccentrically; this means the two gears’ centers do not coincide. The outer gear has teeth that extend inward, meshing with the inner gear’s outward-facing teeth.
One significant difference in the operation of internal gear pumps compared to external gear pumps is the crescent-shaped seal between the gears. This seal acts as a barrier that traps the fluid, carrying it through the pump from the inlet port to the outlet port. As the gears rotate, the volume of the spaces between the teeth changes, which creates suction at the pump inlet and pressure at the outlet.
Internal gear pumps are particularly useful for handling thicker fluids such as chemicals, paints, and adhesives. They are also used in applications requiring a smoother flow or more precise flow control, such as in chemical and food processing industries. These pumps are known for their quiet operation and ability to handle a wider range of viscosities compared to external gear pumps.
Applications and Benefits
Both types of gear pumps are essential in many sectors due to their ability to handle a variety of fluids and operate at high pressures. Gear pumps are commonly found in the mobile and industrial hydraulic systems, including lifting equipment, earthmoving machinery, and in factories where hydraulic equipment is used for production processes.
The choice between an external and internal gear pump often comes down to the specific application requirements such as fluid viscosity, pressure, and the necessity for quiet operation. Both types offer high efficiency and reliability, but internal gear pumps provide an edge in applications requiring less noise and the handling of thicker fluids.
In summary, gear pumps, whether external or internal, are fundamental components in the world of hydraulics, helping power a vast range of machinery with efficiency and reliability. Their robustness, simplicity, and adaptability to different environments make them indispensable in industries across Canada and globally.
2. Vane Pumps
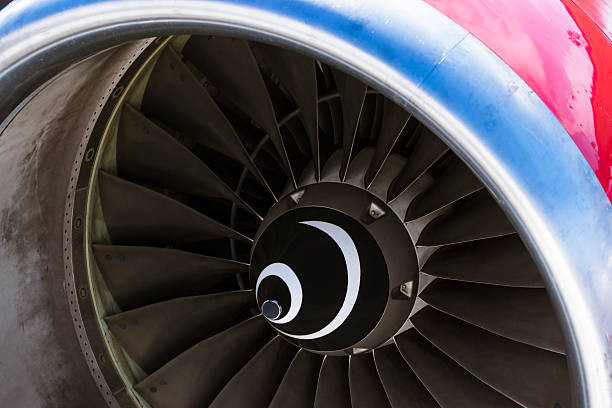
Vane pumps are a type of positive displacement pump used to move fluids through hydraulic systems. The basic mechanism involves a rotor with multiple vanes, housed within an eccentrically positioned cavity in the pump casing. As the rotor spins, the vanes slide in and out, creating expansion and contraction in the volume between the vanes and the casing. This action allows the pump to draw fluid in and then force it out under pressure.
The design of vane pumps enables a continuous flow of fluid, making them highly effective for systems requiring a steady hydraulic pressure. This continuous flow is less pulsative compared to other pump types, such as gear pumps, which translates into smoother operation and less stress on system components.
Types of Vane Pumps
Vane pumps are classified primarily into two types:
Fixed Displacement Vane Pumps:
These pumps deliver a constant amount of fluid with each rotation, which simplifies the design and control of the hydraulic system. They are known for their durability and are widely used in moderate pressure systems such as automotive power steering and air conditioning units.
Variable Displacement Vane Pumps:
More sophisticated than their fixed counterparts, variable displacement vane pumps can adjust the flow and pressure according to the system’s demands. This feature is controlled by changing the eccentricity between the rotor and the casing. These pumps are ideal for applications requiring variable hydraulic flow and high efficiency, such as in plastic injection molding machines and material handling equipment.
Advantages of Vane Pumps
Vane pumps offer several benefits that make them a preferred choice in many hydraulic systems:
- High Efficiency: They maintain excellent operational efficiency over a wide range of viscosities and temperatures. This adaptability is due to the vanes’ ability to adjust to the casing, ensuring minimal leakage and maintaining performance even as parts wear down.
- Low Pulsation and Noise: The smooth flow characteristics of vane pumps result in lower pulsations and reduced noise levels during operation, contributing to a more stable and quieter system environment.
- Durability and Reliability: Vane pumps are robust due to their simple and effective design. The minimal number of moving parts reduces the likelihood of mechanical failures, thereby enhancing the pump’s lifespan and reliability.
- Ease of Maintenance: The design of vane pumps allows for easy access to internal components, facilitating straightforward maintenance and repairs without the need for specialized tools or extensive system downtime.
Applications of Vane Pumps
Vane pumps are used in a myriad of applications, emphasizing their adaptability and efficiency:
- Automotive Industry: They are a staple in power steering systems, providing the necessary hydraulic force to assist in steering maneuvers. Additionally, they are used in transmission and engine cooling systems.
- Industrial Applications: In industries where hydraulic systems are pivotal, vane pumps are used for machine tool operation, automated production lines, and lifting equipment.
- Energy Sector: Vane pumps handle fuel management operations, including the transfer and metering of petroleum products, due to their capability to manage a range of fluid viscosities and maintain precise flow rates.
- Mobile Equipment: They are employed in construction and agricultural machinery, where consistent hydraulic power is critical for functionality and efficiency.
Related: Hydraulic Repair Experts Near British Columbia Canada
3. Piston Pumps
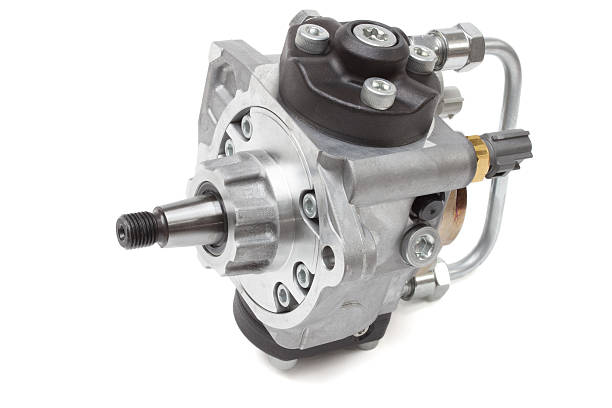
Piston pumps are a type of hydraulic pump that use pistons driven by a rotating shaft to move fluid through a system. These pumps are known for their ability to handle high pressures and variable flow rates, making them suitable for a wide range of applications. The basic operation involves pistons moving back and forth within a cylinder block to draw in and then push out hydraulic fluid, converting mechanical energy into hydraulic energy.
Types of Piston Pumps
Piston pumps can be divided into two main categories based on the arrangement of the pistons: axial and radial.
Axial Piston Pumps:
Axial piston pumps feature pistons that are arranged parallel to the drive shaft. There are two key designs within this category:
Swash Plate Design:
In this common type, the pistons press against a swash plate, which is angled relative to the drive shaft. As the shaft rotates, the swash plate’s angle causes the pistons to move in and out. The angle of the swash plate can often be varied, allowing control over the pump’s output flow and pressure.
Bent Axis Design:
This design involves pistons connected directly to the drive shaft via a bent axis. The angle between the shaft and the pistons allows for piston movement as the shaft rotates. This type is known for its durability and higher efficiency at extreme pressures.
Radial Piston Pumps:
In radial piston pumps, the pistons are arranged perpendicularly to the drive shaft. As the shaft rotates, it drives an eccentric cam, which moves the pistons in and out. This type is particularly effective for very high pressure and low flow applications, and it’s valued for its smooth operation and reliability.
Advantages of Piston Pumps
Piston pumps are preferred for several compelling reasons:
- High Pressure Capability: They can operate under higher pressures than other pump types, such as gear or vane pumps, making them ideal for industrial applications requiring intense pressure.
- Variable Displacement: Especially with axial piston pumps, the ability to adjust displacement allows for precise control over flow rates and system pressures, enhancing system efficiency.
- Durability: Both axial and radial piston pumps are built to last, even under challenging conditions, reducing downtime and maintenance costs.
Applications of Piston Pumps
Due to their robust nature and adaptability, piston pumps are used in a variety of settings:
- Construction and Mining: They power machinery such as excavators, cranes, and loaders where precise movement and high force are necessary.
- Manufacturing: Used in presses and injection molding machines where high pressure and accuracy are crucial.
- Aerospace: Essential for hydraulic systems in aircraft and spacecraft, where reliability and performance are critical.
- Marine: Employed in ships for steering gears and other heavy-duty hydraulic systems.
Related: Expert Hydraulic Repair Services in British Columbia: Ensuring Efficiency and Reliability
4. Screw Pumps
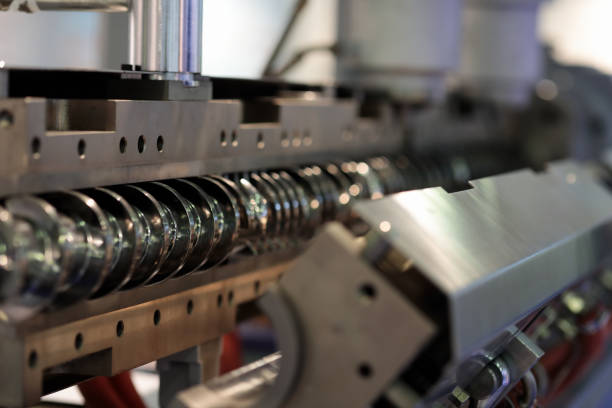
Screw pumps are a type of positive displacement pump that uses one or more screws to move fluids along the pump’s axis. As the screws rotate, they drive the fluid through the pump, providing a smooth and continuous flow. This design is ideal for handling viscous fluids or those containing suspended solids without the risk of clogging. Screw pumps are commonly used in industries such as oil and gas, wastewater treatment, and chemical manufacturing due to their efficiency in transferring thick liquids at a consistent rate.
Key Features and Applications:
- Smooth Flow: The continuous rotational movement of the screws offers a very steady flow, making screw pumps ideal for applications sensitive to pulsations.
- High Viscosity Capability: They can efficiently pump high-viscosity fluids such as heavy oils, bitumen, or molasses, which are challenging for other types of pumps.
- Industries Served: Due to their robust design and ability to handle complex fluids, screw pumps are extensively used in industries like oil and gas, chemical processing, and wastewater management.
5. Bent Axis Pumps
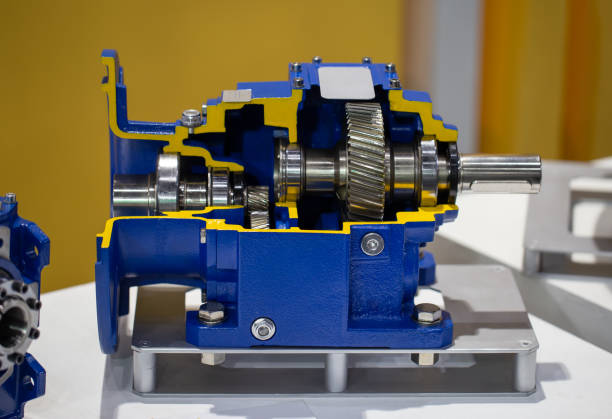
Bent axis pumps are robust hydraulic pumps known for their high efficiency and adaptability to high pressures. The design involves the axis of the pump being bent relative to the drive shaft, which allows the pump to convert rotational motion into fluid power effectively. This type of pump is capable of operating under severe conditions and is commonly used in mobile hydraulic applications, such as construction machinery and industrial vehicles, where reliability under pressure is crucial.
Key Features and Applications:
- High Pressure and Efficiency: Bent axis pumps are known for their ability to work under extremely high pressures, which is a significant advantage in many industrial and mobile applications.
- Durability: The unique design minimizes wear and extends the lifespan of the pump, even under tough operating conditions.
- Industries Served: These pumps are commonly found in construction machinery, agricultural equipment, and other mobile applications where reliable hydraulic power is necessary for efficient operation.
Related: Hydraulic Repair Experts Near British Columbia Canada
6. Peristaltic Pumps
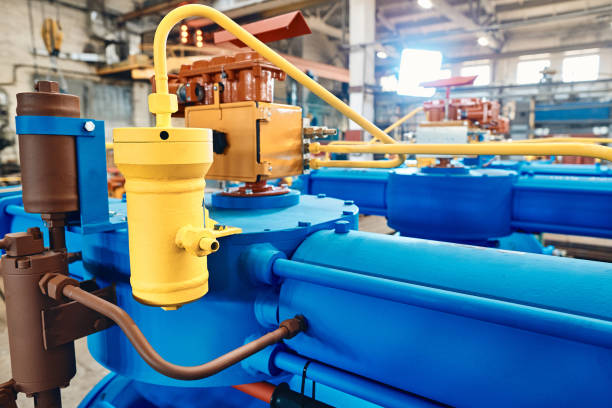
Peristaltic pumps operate by compressing a flexible tube or hose fitted inside a circular pump casing. As the rotor turns, it pinches the tube, pushing the fluid within to move along. This “peristaltic” action makes these pumps ideal for pumping sterile, corrosive, or abrasive fluids because the fluid does not come into contact with the pump mechanism. Applications include medical, laboratory, and chemical processing environments where contamination must be avoided, and precise dosing is required.
Key Features and Applications:
- Contamination-Free: The fluid being pumped does not come into contact with any moving parts of the pump, which avoids contamination. This is crucial in medical, pharmaceutical, and food industries.
- Handles Abrasive or Corrosive Fluids: Peristaltic pumps are excellent for pumping abrasive or corrosive fluids, as the only pump part in contact with the fluid is the hose or tube.
- Ease of Maintenance: The simplicity of the hose or tube replacement makes maintenance quick and straightforward.
- Industries Served: They are widely used in chemical processing, water treatment, and laboratory environments where precision dosing and fluid integrity are paramount.
Wrapping Up
We’ve uncovered the distinct roles and functionalities of gear, vane, piston, screw, bent axis, and peristaltic pumps, each catering to specific industrial needs with precision and efficiency. Understanding these variations is crucial for choosing the right hydraulic pump to meet the demanding requirements of your machinery.
At Delange’s Industries, we are committed to enhancing the performance and longevity of your hydraulic systems. Our extensive services, from onsite hydraulic repair to meticulous hydraulic maintenance, ensure your operations run smoothly with minimal downtime. Whether it’s replacing hydraulic seals or customizing webbing straps, our expertise covers all aspects of hydraulic care. Serving across Canada, Delange’s Industries provides reliable, swift, and comprehensive solutions tailored to maintain and improve your hydraulic systems, ensuring they perform at their best when you need them most.
Related: Expert Hydraulic Repair for Abbotsford’s Commercial and Residential Customers